Chmel se v převážné míře pěstuje na vysokých konstrukcích (7 m), v poslední době se ověřuje pěstování na nízkých konstrukcích (3 m) viz obr. 1. Chmel je hlubokokořenící vytrvalá a popínavá rostlina, která na stanovišti vydrží 20 až 25 let. Sklizeň probíhá ve třetí dekádě srpna a začátkem září. Ke sklizni se přistupuje po dosažení tzv. technické zralosti. V této době jsou chmelové hlávky dokonale uzavřené, při zmáčknutí pružné, jasně žlutozelené s přirozeným leskem a mají pravou jemnou chmelovou vůni. Z chmelnic se chmelové révy sváží na stacionární pracoviště, kde probíhá následné česání, sušení a konečné zpracování produktu.
Historický pohled na používanou mechanizaci
Od 18. století do 1. poloviny 20. století byly pro práci ve chmelnicích využívány jednoduché stroje a zařízení, kde dřívější lidská síla byla nahrazena koňským potahem. Mezi potažní zařízení patřily dřevěné voznice (užívané pro postřiky chmele před chorobami a škůdci), dřevěné brány a válce, dřevěné plečky a jednoduchá plužní tělesa, sáně a rovněž vozy se žebřinami. Ve druhé polovině 20. století se již ve chmelnicích objevily lokomobily pro pohon stacionárních strojů a pásové traktory střídané traktory kolovými. K ručnímu česání chmele se používaly proutěné koše a nůše i různé míry na chmel – věrtele. Forma sklizně chmele pomocí ručního česání již naprosto zanikla. Podstatným důvodem byla produktivita práce, která je u této technologie sklizně nízká. Konzervace chmele se provádí již od minulosti sušením. Zpočátku se chmelové hlávky sušily rozložením na podlaze nebo na lískách. Byly využívány půdní prostory zemědělských usedlostí s typickými větracími otvory ve střešních podhledech. Později se pro urychlení sušení pod lískami začalo topit. Lísky s čerstvým chmelem byly nejdále od topeniště a v průběhu sušení se k němu přibližovaly. Doprava chmele mezi podlažími probíhala za pomocí výtahového zařízení (rumpálu) a v rámci podlaží vozíky. Usušené hlávky byly skladovány v jutových žocích. Od 19. století se začínají používat komorové sušárny, kde byl chmel ve 3 až 4 vrstvách nad sebou na žaluziích, které dovolovaly snadnou manipulaci.
Po druhé světové válce bylo nutné zredukovat plochy starých a neudržovaných chmelnic až o 30 %, v roce 1948 bylo vše znárodněno, pěstitelé byli donuceni vstoupit do JZD a státních statků a vznikly tak velké plochy chmelnic. Došlo k úspěšnému zavádění tzv. širokých sponů se šířkou meziřadí 2,60–2,80 m a vzdáleností v řadě 1,00–1,10 m. Široké spony byly kombinovány se čtyřprutovým zaváděním výhonů, vždy po dvou na dva chmelovodiče, umístěné do tvaru písmene „V” z řadu. Počet zavedených výhonů vzrostl proti původní technologii přibližně o 5 000, takže dosáhl na 1 ha téměř 14 000 zavedených výhonů. Zvýšený počet zavedených rév byl jedním z rozhodujících činitelů podstatného zvýšení výnosů u širokých sponů výsadby. Široké spony se staly základem pro rychlé zavádění mechanizace do výroby chmele. Meziřadí v širokých sponech umožňuje využití běžných kolových traktorů s nesenou nebo taženou technikou k zajištění všech orebních a kultivačních zásahů nejen na podzim a na jaře, ale také po celou dobu růstu chmele, od jeho zavedení až po sklizeň (Rybáček a kol., 1980).
Nízká produktivita ruční práce u většiny technologických operací při pěstování, sklizni a posklizňové úpravě chmele vedla v posledních 40–60 letech k výraznému tlaku na vývoj a výrobu odpovídající techniky.
K orbě a následné kultivaci se používá široká nabídka traktorových souprav se speciálními pluhy, kypřiči a branami. Pro výsadbu sádí nebo kořenáčů poloautomatické sázecí stroje a mechanické ořezávače chmelových babek pro sloupové a mezisloupové řady.
Pro zavěšování chmelovodičů na vysokou chmelnicovou konstrukci se již běžně využívá pracovních plošin nesených na traktoru. Intenzivně se pracuje na vývoji poloautomatického a automatického zavěšovače chmelovodičů a způsobu jejich uchycení na nosnou konstrukci. Při následných dvou technologických operacích je však stále potřeba využít skupinovou brigádnickou pomoc pro manuální práce spojené se zapichováním chmelovodičů a následným zaváděním chmelových rév. Tato činnost odpadá při pěstování chmele v nízké konstrukci. Zdokonalila se technika pro aplikaci hnojiv a pesticidních látek (nesená rozmetadla minerálních hnojiv a tažené ev. samojízdné rosiče).
V letech 1950–1960 nastal rozhodující rozvoj stacionárních česacích linek chmele, jejichž základní principy se používají v moderních zařízeních ještě dnes. První česací stroj na chmel byl do Československa dovezen v roce 1954 z Anglie od firmy Bruff. První zkoušky prokázaly, že mechanizovaná sklizeň žateckého chmele těmito stroji je možná. Technika však musela být přizpůsobena specifickým vlastnostem žateckého chmele, velmi krátkému česacímu období a velké koncentraci ploch. V roce 1959 byl vyroben prototyp první české česací linky na chmel typu ČCH-1. Dále následovaly typy ČCH-2, ČCH-3, ČCH-4, LČCH-1 a LČCH-2. Na první lince bylo potřeba ještě cca 30 obsluhujících pracovníků, ale oproti ruční sklizni to bylo výrazné posílení produktivity práce (Vent, Makovec, Libich, 1970). Od tohoto okamžiku probíhal plynulý vývoj techniky pro česání a čištění chmele až k dnešnímu stupni rozvoje, kdy nepoměrně výkonnější linky vyžadují obsluhu max. 4–6 pracovníků. Nové linky již splňují náročné kvalitativní parametry na maximální čistotu a minimální poškození chmelových hlávek. Výkonové parametry linek vyžadují odpovídající organizaci práce, která spočívá v zajištění stálého přísunu čerstvého chmele bez prostojů linek. U nízkých konstrukcí se využívá tažený sklízeč, který na poli sčesává hlávky společně s částmi biologických příměsí a směs je odvážena na separační linku k dokončení procesu čištění.
Vysoká výkonnost česacích linek vyžaduje odpovídající sušicí kapacitu s minimální výkonností 750 až 900 kg.h-1 zeleného chmele. Tomu v našich podmínkách v současné době odpovídají pásové sušárny a nově komorové boxové sušárny (Jech a kol., 2011). První pásová sušárna k nám byla dovezena v roce 1959 a umožňovala již kontinuální sušení až do konečného stavu bez zásahu člověka. V současné době se používají modernější typy pásových sušáren s výkonností 750 a 900 kg.h-1. Z důvodu malé skladovací kapacity sklizňových středisek je nutné usušený chmel okamžitě lisovat do hranolů příp. žoků a dopravit do klimatizovaných skladů zpracovatelské linky. V České republice existují dvě zpracovatelské linky, kde je chmel následně zpracován s vyústěním v granulaci a balení chmelového produktu. Naprostá většina odběratelů (pivovarů) využívá ke chmelení granule, pouze výjimečně se využívají lisované chmelové hlávky. Pozdější vývoj v extrahování pivovarsky cenných látek u nás nenalezl uplatnění.
Výrobní technologie
V rámci výrobní technologie ve chmelařství se musí maximálně přizpůsobovat technická řešení strojních linek a biologické, chemické a ekonomické ukazatele pěstovaných odrůd. Výrobní technologie se člení na čtyři základní úseky: zakládání chmelnic, pěstitelská technologie chmelových porostů, technologie sklizně a technologie posklizňové úpravy hlávek. Další rozvoj chmelařství si vynucuje trvalou inovaci výrobních postupů zahrnující šlechtění nových odrůd a efektivní pěstitelské operace vyúsťující do vysoké kvality konečného produktu. Pro pěstitele to znamená maximální snižování cen vstupů a co největší zhodnocení finálních produktů. Logicky z toho vyplývá, že se další rozvoj efektivního pěstování chmele neobejde bez ještě širšího a inovativnějšího využití stávajících a nově vyvíjených mechanizačních prostředků, a to i pro operace, kde doposud ruční práce převládá. Při volbě celé výrobní technologie je tedy nutné, při akceptování celosvětové konkurence, vycházet nejen z obecně známých agrotechnických hledisek, ale více než kdy jindy z dostupné mechanizace na trhu, která však musí být pro pěstitele finančně přijatelná.
Pracovní postupy úpravy chmele na stacionárním pracovišti
U chmelu pěstovaného na vysoké konstrukci (7 m) se při sklizni chmelové révy odstřihávají 1,2–1,3 m nad zemí (těsně pod spodními plodnými pazochy), strhávají ze stropu konstrukce a nakládají na speciální traktorový návěs. Převládá mechanizované odstřihávání a strhávání pomocí strhávače umístěném na traktoru. Révy jsou ihned dopravovány k česací lince. Dovážené révy musí být čerstvé, nezavadlé, s optimální sklizňovou vlhkostí 72–82 %. Interval mezi odstřihnutím a česáním by měl být co nejkratší, jelikož zavadlé hlávky jsou při česání více poškozovány. Je proto nezbytné dopravu rév a vlastní česání organizačně sladit.
Na stacionárním pracovišti se dokončuje sklizňový proces spočívající v česání a čištění, příp. jenom čištění chmelových hlávek. Konečný produkt (hlávky) se následně v posklizňové lince pěstitele suší, klimatizuje a balí pro přepravu do centrální zpracovatelské linky. Cílem pracovního postupu na stacionárním pracovišti je získat kvalitní nepoškozené hlávky s minimem ztrát a příměsí ve finálním produktu.
Pracovní postupy a operace úpravy chmele můžeme rozdělit na:
A) Pracovní postupy a operace u pěstitele chmele:
- česání a čištění,
- sušení, klimatizace a balení.
- příjem, homogenizace, sušení, čištění, granulace a balení.
B) Pracovní postupy a operace v centrální zpracovatelské lince:
Česání a čištění chmele
Česání a čištění se uskutečňuje na strojní lince u pěstitele, kam jsou plynule dováženy chmelové révy z vysokých chmelnic. Z nízkých chmelnic je na stacionární pracoviště dovážena směs hlávek, listů a pazochů a zde dochází pouze k čištění chmele. Operace česání a čištění se uskutečňují v česacích strojních linkách, které se do r. 1990 vyráběly v Agrostroji Prostějov. Posledním typem byla česací linka LČCH-2, která je dodnes nejpoužívanější. Po roce 1990 zajišťuje kompletní techniku pro chmelaře Chmelařství, družstvo Žatec, závod Mechanizace. V roce 1995 se začala vyrábět česací linka AT-50 výkonnostně určená pro velké plochy (až 100 ha), potom následovaly linky PT-15 (15-20 ha) a PT-30 (až 40 ha) viz obr. 2.
U pěstitelů jsou v současné době česací linky poměrně zastaralé, jejich modernizace a obměna probíhá velice pozvolna. Téměř 60 % česacích linek jsou linky provozované 20 let a více. Zastaralé linky jsou méně výkonné a více poruchové. I přes pokles provozuschopných česacích linek je možné konstatovat, že v průměru jejich vytíženost není stoprocentní vzhledem k postupně klesající celkové výměře chmelnic. Nejvíce výrazný úbytek lze pozorovat u strojů LČCH-1, které absolutně nesplňují požadované parametry na kvalitu česání a mají vysoké provozní náklady. Stroje LČCH-2 naopak po modernizaci mohou výkonnostně a ekonomicky zdatně konkurovat novým česacím linkám, a proto se touto cestou, z důvodu omezených finančních možností, vydává řada pěstitelů (Podsedník a kol., 1996).
Sušení, klimatizace a balení chmele
Chmel je třeba bezprostředně po očesání zakonzervovat a zabránit tak jeho znehodnocení. Očesané hlávky intenzivně dýchají, zvyšují teplotu a hrozí nebezpečí jejich zapaření až znehodnocení, což může vést ke ztrátě lesku, změně základní barvy a k negativnímu dopadu na celkovou kvalitu hlávek. Proto musí být urychleně započato s jejich sušením. Interval mezi česáním a sušením nemá překročit 2 hodiny a je nutné organizačně sladit proces česání a sušení včetně výkonnosti obou zařízení. Vlastní sušení probíhá u pěstitelů buďto ve starších komorových (sesypných žaluziových) sušárnách nebo novějších pásových (kontinuálních) sušárnách (obr. 3). V poslední době je trend opět využít nový způsob komorového (tzv. vsázkového) sušení (obr. 4). Hlávky se suší při teplotě 55–60 °C po dobu 6–9 hodin. Při teplotě nad 60 °C dochází ke zhnědnutí lupulinu. V průběhu sušení musíme zajistit dokonalou cirkulaci sušícího vzduchu a dokonalý odvod uvolněné vlhkosti, aby nedocházelo k zapaření hlávek. Proces vysychání není rovnoměrný, ale prochází několika stádii – vysušením listenů, vysušením stopek a nakonec vysušením vřeténka. Vysušení listenů, vzhledem k jejich velkému povrchu a malé tloušťce, nastává jako první. Druhá se usuší stopka a poslední v řadě je vysušení vřeténka, tedy nejhůře dostupné části chmelové hlávky.
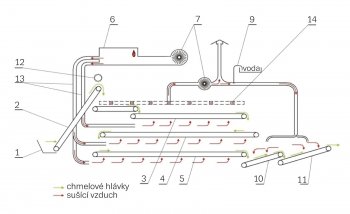
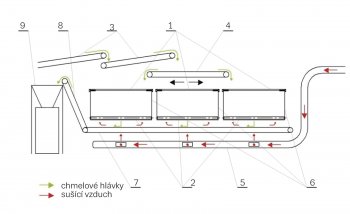
Při sušení chmele rozlišujeme stejně jako u sušení jiných plodin tři fáze. První fází je fáze ohřevu materiálu, kdy se přivádí teplo, které je spotřebováváno a tato fáze končí ve chvíli, kdy nastane tepelná rovnováha mezi teplem předávaným a výparným. Následuje fáze stálého sušení materiálu, kdy se teplota sušení udržuje na té úrovni, které dosáhla na konci první fáze, tedy ohřevu materiálu. Tato končí dosažením tzv. kritické vlhkosti, kdy se povrch sušených hlávek chmele chová jako volný povrch vody a napětí vodních par nad povrchem sušeného materiálu je stejné jako napětí nad volným povrchem vody. V konečné fázi procesu sušení nastává pokles rychlosti sušení, neboť přívod vody z vnitřních partií chmelové hlávky již není dostatečný, neustále se zpomaluje a při rovnovážné vlhkosti se zcela zastaví. Nejdůležitější parametry ovlivňující průběh sušení i jeho konečný výsledek jsou teplota sušení, množství vzduchu a jeho rychlost proudění, specifické vlastnosti chmelových hlávek a ostatní činitelé (výška vrstvy sušeného chmele, doba sušení, rychlost průchodu chmele jednotlivými částmi sušárny).
Aby se usušení podařilo, je nutné chmel usušit na vlhkost 5–7 %. Usušení na tuto vlhkost ale přináší velkou nevýhodu v podobě křehkosti chmelové hlávky a vysoké lámavosti. Náchylností hlávek k rozpadu může docházet k odrolu listenů od vřeténka a také k odpadu lupulinových žlázek z povrchu listenů. Tato nevýhoda je odstraňována následnou klimatizací chmele.
Klimatizací se chmel zvlhčuje na vlhkost 10–12 %, a tím se minimalizuje jeho znehodnocení při lisování a následném skladování v žocích a hranolech. Při vlhkosti hlávek 5 až 7 % jsou hlávky křehké, snadno se rozpadají a poškozují a nejsou schopné další manipulace. Usušení hlávek přímo na vlhkost 10–12 % se prozatím neprovádí, protože by při této vlhkosti nebylo úplně usušeno (umrtveno) vřeténko. Úpravu vlhkosti můžeme zajistit různým způsobem:
- Po usušení ve starší komorové (žaluziové) sušárně necháme hlávky v nižší vrstvě na podlažích půdního prostoru navazujícího na komorovou sušárnu. Suché hlávky přijímají vlhkost z okolního prostředí, opatrně je převrstvujeme a podle potřeby jemně kropíme vodou. Tento proces probíhá 2–4 týdny. U nových komorových (vsázkových) sušáren dochází po usušení chmele k obdobnému ustálení avšak přímo v sušících komorách a jeho přirozenému zvlhčení.
- Klimatizací chmele v klimatizační komoře, tj. v zařízení přímo navazujícím na pásovou sušárnu. Hlávky jsou zvlhčovány vzduchem o relativní vlhkosti 70–75 % po dobu 70–90 minut.
Po klimatizaci pak bezprostředně následuje lisování chmele a hlávky se balí do transportních obalů (žoků) o rozměrech cca 0,8 × 2 m. Hmotnost naplněného žoku činí 60–70 kg. Stále více se rozšiřuje lisování a balení do hranolů (kvádrů) o rozměrech 0,6 × 0,6 × 1,2 m s maximální hmotností 60 kg a možností jejich paletování. Podle zákona o ochraně chmele je každý obal zvážen, opatřen štítkem s potřebnými údaji a zaplombován. Toto označování chmele (tzv. známkování) musí zajistit pravost původu vypěstovaného chmele. Jednotlivé chmelnice se totiž od sebe liší kvalitou konečného produktu. Takto zabalené hlávky jsou odváženy do centrální zpracovatelské linky nebo se před expedicí dočasně skladují u pěstitele.
Centrální zpracovatelská linka
Chmel dovážený v žocích nebo hranolech od pěstitelů ke zpracování je podle přání obchodníků a potažmo pivovarů na příjmu míchán tak, aby byl respektován požadovaný původ chmele a zajištěna kvalita vyjádřená podílem alfa hořkých kyselin. Kvalita chmele je na příjmu ověřována odběrem vzorků z jednotlivých obalů.
Dříve se chmel balil ve své nejjednodušší a nejstarší formě tj. jako hlávkový chmel. Hlávky se třídily podle přání zákazníka, konzervovaly sířením a slisovaly do přepravních obalů. Delším skladováním však docházelo k oxidaci a následnému snižování obsahu hořkých látek. Pro tyto nevýhody a velký skladovací objem tato forma balení výrazně poklesla.
Granulace chmele je novější a současně nejrozšířenější forma úpravy a balení. Využívá se k tomu centrální zpracovatelská linka (obr. 5), kam se chmel dováží ze všech pěstitelských oblastí. Hlávky se homogenizují, zbaví nečistot a suší na vlhkost 6,5–7,0 %. Dále jsou jemně rozemlety, slisovány do granulí o průměru 6 mm a baleny v inertním prostředí (CO2, N2) do folií. Jednotlivé sáčky o různé požadované hmotnosti jsou vkládány do kartonů a ukládány na paletu. Takto upravené hlávky lze v inertním prostředí skladovat i delší dobu, menší objem má výhody pro dopravu i skladování a je zde větší využitelnost hořkých látek z granulí v průběhu chmelovaru.
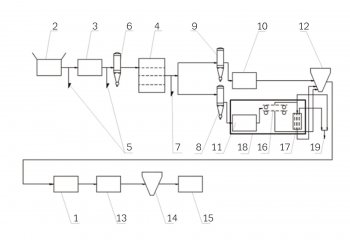
Granulovaný chmel je upravován dvojím způsobem:
- granule typ 90 – složení je téměř shodné s hlávkovým chmelem, ze 100 kg hlávek se získá přibližně 90 kg granulí,
- granule typ 45 – dokonalejším oddělením balastních látek z hlávky se získá produkt přibližně s dvojnásobným obsahem hořkých látek. Ze 100 kg hlávek se získá přibližně 45 kg granulí, výsledný objem produktu je jen 40–50 % původního objemu.
Směry dalšího vývoje
Chmelařská mechanizace je neustále se rozvíjející obor, ve kterém se hledají nové principy a uplatňují nová technická řešení strojů pro jednotlivé pracovní operace tak, aby se maximálně vyloučila ruční práce a zajistila co nejlepší kvalita finálního produktu při snižování vstupů do výroby. Nová a moderní technika také potřebuje kvalifikované uživatele, kteří rozhodují o jejím nasazení, seřízení a využití.
Chmel je tradiční českou plodinou, která má pro své specifické vlastnosti významné postavení ve světě a u které více jak 80 % produkce je vyváženo do zahraničí. Světové konkurenční prostředí o to významněji zpětně působí na české pěstitele. Snižování výrobních nákladů a zvyšování kvality finálního produktu se vedle cen nutných vstupů (investice, energie, hnojiva, pesticidy, náhradní díly, lidská práce aj.) prolíná celou technologií, tj. výběrem odrůd, založením porostu, pěstitelskými, sklizňovými a posklizňovými operacemi a konečnou úpravou chmele (Rybka a kol., 2008).
S požadavkem na větší odrůdovou rozmanitost, specifické vlastnosti a vyšší výnos se rozšiřuje, vedle stále nejvíce rozšířeného Žateckého poloraného červeňáku (v současnosti cca 87 % výměry), pěstování vyšlechtěných hybridních odrůd. Tyto odrůdy se v některých biologických znacích a růstových vlastnostech odlišují od klasických odrůd a ty je pak nutné respektovat při jejich pěstování a dalších operacích. Z pohledu stacionární techniky, která se tomu musí přizpůsobit, se jedná hlavně u česací linky o větší množství nadzemní biomasy a vyšší výnos a dále u sušáren je to zvýšený obsah lupulinu v hlávkách a to vyžaduje i určitou úpravu sušícího procesu.
Produktivita práce, snižování ztrát a kvalita konečného produktu jsou hlavní kritéria jednotlivých výkonnostně na sebe navazujících strojních linek na stacionárních pracovištích. Stále větší důraz, zvláště zahraničních odběratelů chmele, je kladen na kvalitu a perfektní čistotu konečného produktu, což musí vést jednoznačně k absolutnímu eliminování nečistot v technologickém procesu. Řešením je volba optimální technologie a detailních úprav strojů ve stacionárních linkách. V blízké budoucnosti jistě dojde ke zkvalitnění technologie úchytu chmelovodičů k chmelnicové konstrukci, k šetrnějšímu sušení chmele s větším využitím automatizačních prvků (zvláště u hybridních odrůd), ke zlepšení kvality obalového materiálu pro dopravu slisovaného chmele od pěstitelů do centrální zpracovatelské linky a také musí podstoupit revizi i celý technologický tok materiálu ve zpracovatelské lince s důrazem na kvalitu finálních produktů.
Tento příspěvek vznikl za přispění MZe ČR jako součást řešení výzkumného projektu NAZV č. QJ1510004.
Literatura:
[1] HEŘMÁNEK, P., RYBKA, A., HONZÍK, I., VENT, L., JOŠT, B. 2012. Separation of impurities from dry hops. Jelgava: Proceedings of 11th International Scientific Conference. Latvia University of Agriculture, Faculty of Engineering. May 24-25, 2012, pp. 117-121.
[2] JECH, J. a kol. 2011. Stroje pre rastlinnú výrobu 3 - Stroje a zariadenia na pozberovú úpravu rastlinných materiálov a na ich skladovanie. Praha: Profi Press s.r.o., 2011, 368 s. ISBN 978-80-86726-41-0.
[3] KROFTA, K., JEŽEK, J., KLAPAL, I., KŘIVÁNEK, J., POKORNÝ, J., PULKRÁBEK, J., VOSTŘEL, J. 2012. Integrovaný systém pěstování chmele. Metodika pro praxi. Žatec: Časopis Chmelařství – Petr Svoboda, 2012, 94 s. ISBN 978-80-86836-82-9.
[4] KUMHÁLA, F., HEŘMÁNEK, P., MAŠEK, J., KVÍZ, Z., HONZÍK, I. 2007. Zemědělská technika. Stroje a technologie pro rostlinnou výrobu. Praha: Powerprint s.r.o., 2007, 438 s. ISBN 978-80-213-1701-7.
[5] NEUBAUER, K., FRIEDMAN, M., JECH, J., PÁLTIK, J., PTÁČEK, F. 1989. Stroje pro rostlinnou výrobu. Praha: SZN, 1989, 720 s. ISBN 80-209-0075-6.
[6] PODSEDNÍK, J. 1996. Mechanizované technologie sklizně chmele, 50–100 ha. Žatec: Chmelařství, družstvo Žatec, 1996, 7 s.
[7] RYBÁČEK, V. a kol. 1980. Chmelařství. Praha: SZN, 1980, 426 s. ISBN 07-068-80.
[8] RYBKA, A., HEŘMÁNEK, P., HONZÍK, I., JOŠT, B., PODSEDNÍK, J., VENT, L. 2012. Ověřená technologie separace příměsí ve stacionární česací lince chmele s využitím nově navržených překulovačů. Smlouva o uplatnění výsledku s firmou CHMEL-Vent spol. s r.o. Kněžice, IČ: 47308141, datum uzavření smlouvy:13. 11. 2012.
[9] RYBKA, A., HEŘMÁNEK, P., HONZÍK, I., JOŠT, B., PODSEDNÍK, J., VENT, L. 2013. Ověřená technologie oddělení hlávek chmele za česacími stěnami česací linky. Smlouva o uplatnění výsledku s firmou CHMEL-Vent spol. s r.o. Kněžice, IČ: 47308141, datum uzavření smlouvy:17. 11. 2013.
[10] RYBKA, A., HEŘMÁNEK, P., HONZÍK, I., JOŠT, B., PODSEDNÍK, J., VENT, L. 2014. The effect of work of inclined belt conveyors on the quality of hop separation in hop picking line. Prague: Plant, Soil and Environment, 2014, vol. 60, No. 4, pp. 184-190, ISSN 1214-1178.
[11] RYBKA, A., HEŘMÁNEK, P., HONZÍK, I., JOŠT, B., PODSEDNÍK, J., VENT, L. 2015. Modernizace technologického postupu pro zvýšení výkonnosti česací linky chmele. Praha: Certifikovaná metodika, ČZU v Praze, 2015, 28 s. ISBN 978-80-213-2554-8.
[12] SRIVASTAVA, A. K., GOERING, C. E., ROHRBACH, R. P., BUCKMASTER, D. R. 2006. Engineering Principles of Agricultural Machines. 2nd Edition. St. Joseph, Michigan, USA: ASABE, 2006, 588 p. ISBN 1-892769-50-6.
[13] STOUT, B. A. et al. 1999. CIGR Handbook of Agricultural Engineering – Plant Production Engineering. St. Joseph, Michigan, USA: ASAE, 1999, 632 p. ISBN 1-892769-02-6.
[14] ŠNOBL, J. Sklizeň a posklizňová úprava chmele. [online]. [cit. 2015-09-21]. Dostupné z: http://etext.czu.cz/php/skripta/kapitola.php?titul_key=17&idkapitola=59
[15] ÚKZÚZ Žatec. 2015. Přehled ploch chmele ČR – podle okresů. Sklizňová plocha chmele ČR – podle odrůd. Stav k 20. 8. 2015. Žatec, 2015, 2 s.
[16] VENT, L., MAKOVEC, K., LIBICH, V. 1970. Mechanizované linky ve chmelařství. Žatec: VÚCH,1973, 141 s.
Autor: doc. Ing. Adolf Rybka, CSc., Česká zemědělská univerzita v Praze, Katedra zemědělských strojů
Fotografie: Archiv autora